Exp 1: Shell and Tube Heat Exchanger
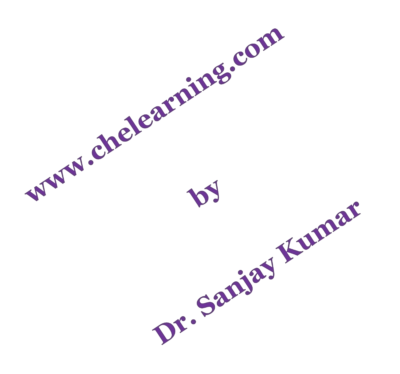
Aim
To determine the overall and individual heat transfer coefficient under thermal steady state conditions.
Apparatus
The experimental setup consists of a shell and tube heat exchanger, with multiple tubes enclosed within a cylindrical shell. The key components include:

- Tube Bundle: A set of tubes through which the cold fluid flows.
- Shell: An outer cylindrical casing that allows hot fluid to flow around the tubes.
- Baffles: Internal structures placed within the shell to enhance heat transfer by directing the shell-side fluid flow and providing mechanical support to the tubes.
- Baffles increase the velocity and turbulence of the shell-side fluid, thereby improving the heat transfer.
- Flow Control System: A cold-water inlet valve allows flow rate regulation.
- Thermometers: Measures the inlet and outlet temperatures of both hot and cold fluids.
- Pump: Facilitates hot water circulation through the shell.
- Hot Water Tank with Heater: Supplies hot water to the shell side of the exchanger.
- The hot water circulates through the shell and returns to the same tank.
- Schematic Diagram: A basic schematic for a single-pass shell-and-tube heat exchanger is shown in the Figure below.

Specifications:
The specifications for the 1-1 Heat exchanger are as follows:
- A 1-1 Heat exchanger refers to a 1-shell, 1-tube pass configuration.
- 1-Shell means a single shell enclosing the tube bundle.
- 1-tube pass means the fluid inside the tubes flows in a single pass from one end to the other end without reversing direction.
Geometric Specifications:
- No. of tube (N) = 37, Shell inside diameter (Ds) = 150 mm, baffle spacing (B) = 200 mm, length of each tube (L) = 600 mm, inner diameter of tube (di) = 9.3 mm, outer diameter of tube (do) = 12.7 mm, tube pitch (square arrangement) P = 23 mm, tube clearance C = (P – do) = 10.3 mm.
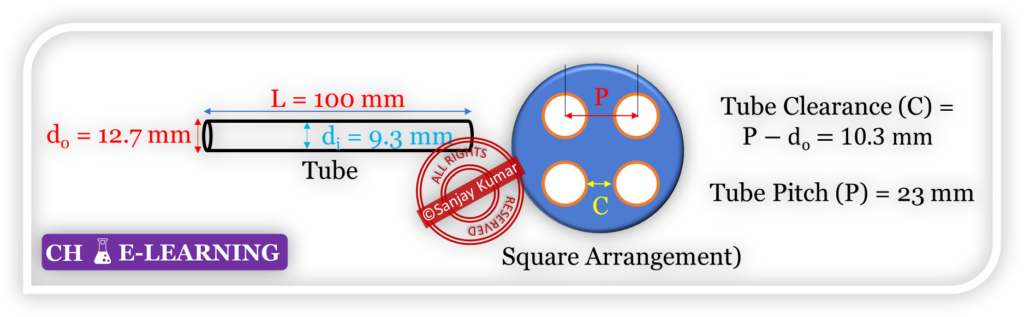
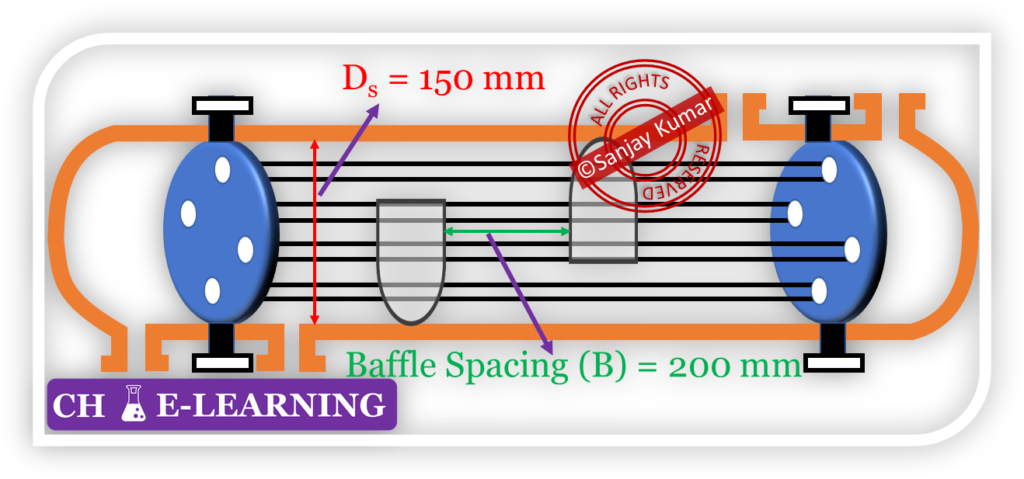
Malarial Properties:
- The shell material is stainless steel, and its thermal conductivity is k = 54 W/m.K
- The tube side material is copper, and its thermal conductivity is k = 386 W/m.K
Experimental Procedure
Steps are given below
Step 1: Hot Water Preparation)
- Fill the hot water tank with water up to approximately ¾ of its capacity.
- Turn on the heater and set the water temperature to 70 °C.
Step 2: Hot Water Circulation
- Once the set temperature (70 °C) is reached, start the pump to circulate hot water through the shell side.
- Wait until a steady-state condition is achieved, i.e., \mathrm{T_H^{In}=T_H^{Out}}
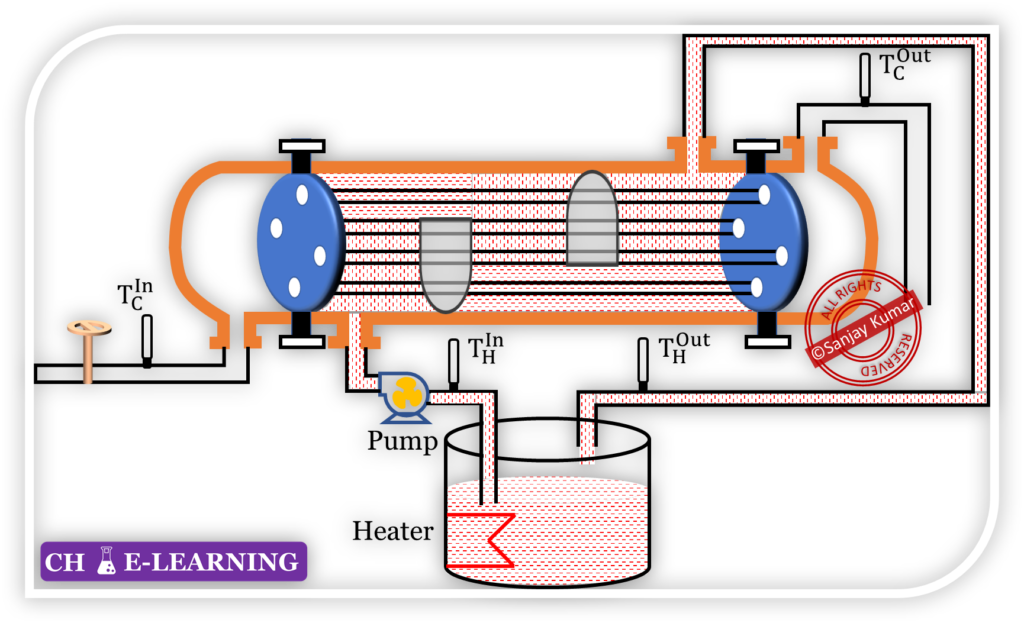
Step 3: Cold Water Circulation
- Open the cold-water inlet valve and adjust the flow rate. Cold water flows through the tube side.
- Monitor the outlet temperature of the cold water until a steady-state condition is achieved, i.e.,
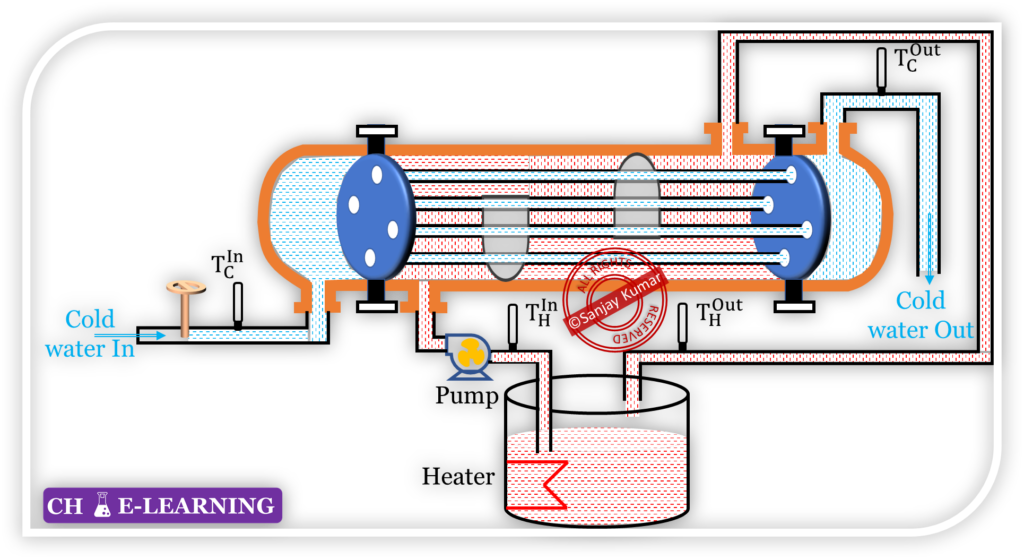
- The flow rate of cold water can be estimated by collecting water for a given time.
Step 4: Data Collection
- Record the inlet and outlet temperatures for both hot and cold water.
Step 5: Repeat the Experiment
- Conduct the experiment for different cold water flow rates and note the readings.